Portfolio
Spray Booths Project
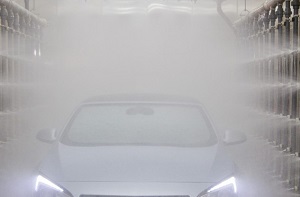
Zytec Systems ltd was employed to develop the PLC & HMI software, test and commission four water spray booths.
A Siemens S7:300 PLC & HMI with local I/O modules are utilized for the control of the System. The system comprises of a common pressurized water supply
from a monitored water tank with automatic top-up facilities.
The two pump sets (one for high pressure tests) were driven by Siemens VSD drives on a profinet network. When a vehicle was required to be tested the operator would move it into the booth and close the roller door. The operator would then select one of the preset six tests and the control system would use PID control to maintain a water pressure at the selected booth for a given test time. As other booths are started then the PID would automatically control to maintain the pressure. Once the test time had elapsed the operator was signaled via a pulsing siren and the relevant roller door would automatically open. The new system is used to verify the water integrity of the vehicles with shower tests lasting typically 24 hours and storm tests lasting typically 1 hour.
------------------------------------------------------------------------------------------------------------------------------
Warehouse Project
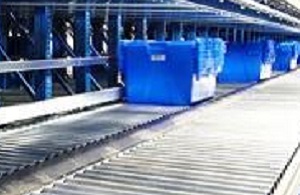
A leading online supermarket employed Zytec Systems ltd to develop the PLC & HMI software and commission a warehouse extension. A Siemens S7:319 PLC with local and Remote I/O modules was utilized for the control of the System. There was two Profibus networks, connecting to the two high density system cranes and six 2-channel ASi controllers which in turn connected to remote I/O.
The system comprised of two automatic cranes that stored totes containing part customer orders. The conveyor system transported the totes to the appropriate crane following manual picking of products. Upon a retrieval request the conveyor system transported the tote to the appropriate shipping lane in a predefined delivery order. This tote was then manually loaded onto a van for delivery . The system was increased to handle 3200 totes per hour to storage and providing an additional 14 shipping lanes doubling the number of vans capable of loading simultaneously.
------------------------------------------------------------------------------------------------------------------------------
Pallet System
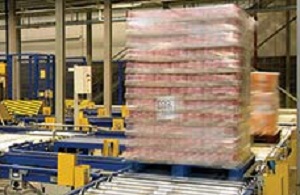
A leading UK Ice Cream manufacturer employed Zytec Systems ltd to develop the PLC software and commission a double Conveyor System to transport pallets carrying production materials between the warehouse and production facilities.
A Rockwell Control Logix PLC with a Rockwell Factory Talk HMI was utilized for the control of the System. The system also included for Remote I/O on a ASI Network
that communicated back to PLC via Ethernet TCPIP. The system also contained a Wifi Remote control for determination of destination of pallets to proceed directly to
the warehouse/production facility or too the high level intermediate store.
The double conveyor system contained a facility which enabled a reverse selection of the conveyors to allow for a line breakdown and still have the facility to transfer
pallets in both directions. The system was designed to achieve a leisurely 50 pallets per hour per line, and was finally commissioned and was achieving over 60 pallets
per hour. The system has now enabled the client to remove pallet trucks being driven across a main road and increased the efficiency of production material planning.
------------------------------------------------------------------------------------------------------------------------------
Racecourse Power
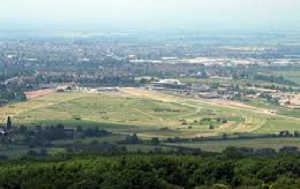
Cheltenham Racecourse employed Zytec Systems ltd to develop the PLC & HMI software and commission an automatic Power Monitoring & Generator Switching System.
A Siemens S7:315 PLC with local/Remote I/O modules was utilized for the control of the System. There is one Profibus network connected to a Fibre-Optic link to remote I/O and remote Siemens OP77A HMI. The system controlled a Generator and eight switchgear systems to enable power restoration during mains failure. A Mains 11kV voltage is monitored and when detected as failed the switching gear operated in a preset sequence to enable the generator to start and then once running and able to accept load the switching gear was enabled.
------------------------------------------------------------------------------------------------------------------------------
Servo Control
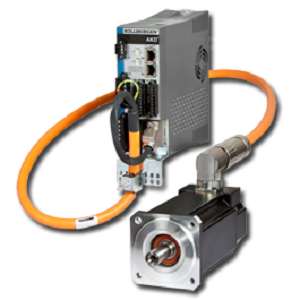
Zytec Systems ltd was employed to develop the PLC & HMI software, test and commission a Fluting rig for fluting the end of Torque Wrench handles. The Fluting rig was contained within a Robot Cell and interface signals was required between the robot and the Rig PLC. A Siemens S7:300 PLC with a Proface GP HMI was utilized for the control of the System. The system also included for Local I/O and a Profibus Network to the Kollmorgen Servo controller, the HMI was connected to the PLC via Ethernet TCPIP.
As the rig was part of a Robot Cell the safety aspect was carefully designed to ensure operator and machine security. The Fluting Rig was replacing a manual fluting operation with mechanical stops which need to be adjusted prior to changing parts. The new system held a database of the different parts and once selected via the HMI, the system would automatically load the data and operate to the new dimensions. This greatly reduced the setting time and parts being produced increased by 45% with the improved automation.
------------------------------------------------------------------------------------------------------------------------------
Data PLC's
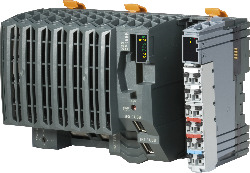
Zytec Systems ltd was employed to develop the PLC software, test and commission nineteen data concentrator PLC's for a household name supplier on their Cheese and Butter lines Each line comprised of a various number of machines to provide differing packaging solutions. The B&R X20 PLC's was utilized for the monitoring of the Lines. Each PLC system monitored the various statuses of all the independent machines within the lines, and reported back to the OEE Impact System via Ethernet TCPIP
Along with these statuses the DCT PLC monitored other inputs to provide throughput data at various stages of the process. Outputs were also utilized to provide line status indication via beacons for operator problem direction. Once the system was installed on all lines, this provided detailed information to the management of production lines effectiveness, along with detailed breakdown information and timings. The system was used to increase productivity and provide detailed analysis of maintenance requirements on the packaging machines by providing the most common faults which could be interrogated and in some cases eliminated. Other benefits included a revision of production procedures which also gave better line efficiency and increased production levels.